우주 탐사선의 금형 유지 보수 사례 연구
1. 우주 탐사선 금형 유지 보수의 필요성: 왜 중요한가?
우주 탐사선은 극한 환경에서 정밀한 성능을 발휘해야 하며, 이 과정에서 금형은 필수적인 역할을 합니다. 탐사선의 주요 부품은 대부분 고정밀 금형을 이용해 제작됩니다. 엔진 부품, 태양광 패널 프레임, 기체 외피 등 우주선의 내구성과 성능은 금형의 품질에 달려 있습니다. 그러나 금형은 반복적인 사용과 극한의 열 및 압력 변화로 인해 마모와 손상이 발생하기 쉽습니다.
실제 사례로, NASA는 화성 탐사선 제작 시 금형의 미세 균열로 인해 부품 변형 문제가 발생한 적이 있습니다. 이 문제는 초기 생산 단계에서 금형 유지 보수가 제대로 이루어지지 않아 발생한 것으로 분석되었습니다. 이러한 사례는 금형 관리가 단순한 제조 공정의 일부가 아니라, 우주 탐사의 성공 여부를 결정짓는 핵심 요인임을 보여줍니다. 우주 탐사선은 높은 신뢰성과 지속 가능성을 요구하기 때문에, 금형 유지 보수의 체계적인 접근이 필수적입니다.
특히, 금형의 마모를 방지하고 수명을 연장하는 방법은 우주 임무의 지속 가능성에도 영향을 미칩니다. 우주선이 극한의 온도 차와 진공 상태에서 작동하는 만큼, 금형의 초기 설계와 관리 방안은 전체 프로젝트의 성패를 좌우하는 중요한 단계입니다. 따라서 우주 탐사선의 제작과 운영에서 금형 유지 보수는 기술적 도전 과제를 넘어 필수 불가결한 요소로 자리 잡고 있습니다.
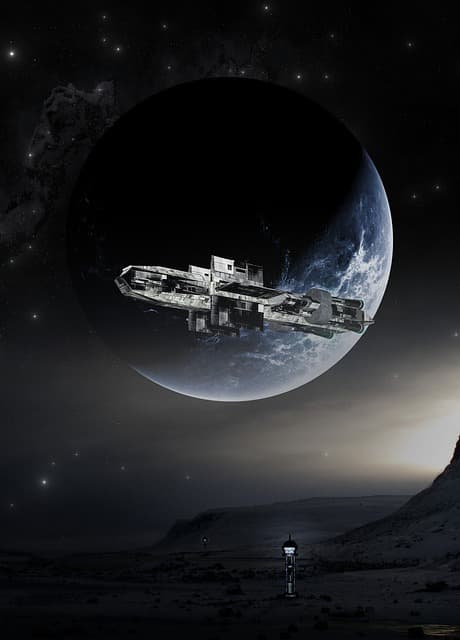
2. 우주 탐사선 제작에서 금형 관리 실패 사례
과거 우주 탐사선 제작 과정에서는 금형 관리 실패로 인해 막대한 비용과 시간이 낭비된 사례가 보고되었습니다. 대표적인 예로, 유럽우주국(ESA)의 한 탐사선 프로젝트에서 금형의 피로 균열을 조기에 발견하지 못해 주요 부품 재제작이 필요했던 사건이 있습니다. 이 과정에서 6개월 이상의 프로젝트 지연과 약 1억 달러의 추가 비용이 발생했습니다.
금형 피로 균열은 일반적으로 높은 압력과 반복적 응력으로 인해 발생합니다. ESA의 사례에서는 금형 상태를 실시간으로 모니터링할 수 있는 기술이 부족했고, 현장 검사가 늦어진 것이 원인이었습니다. 이로 인해 부품의 내구성이 저하되었고, 결과적으로 탐사선 전체의 성능에도 영향을 미쳤습니다.
또한, 실패 사례는 금형 관리가 단순히 유지 보수의 영역을 넘어, 제조 단계부터 통합적으로 관리되어야 한다는 교훈을 남겼습니다. 예컨대, 금형의 사용 주기를 체계적으로 추적하고, 데이터 기반으로 마모 상태를 예측하는 기술이 도입되었다면, 문제를 사전에 방지할 수 있었을 것입니다. 우주산업에서 금형 관리의 중요성은 단순한 비용 절감 이상의 의미를 가지며, 프로젝트 성공률을 높이는 필수 조건입니다.
3. 성공적인 유지 보수 사례: 일본의 하야부사2 프로젝트
일본 우주항공연구개발기구(JAXA)의 하야부사2 프로젝트는 금형 유지 보수의 성공적인 사례로 자주 언급됩니다. 이 프로젝트에서는 금형의 사용 주기와 성능을 모니터링하기 위해 IoT 센서와 AI 기술을 활용했습니다. 금형의 온도, 압력, 마찰력을 실시간으로 추적한 결과, 마모가 시작되기 전에 유지 보수 작업을 실시할 수 있었습니다.
특히, 이 프로젝트에서는 다이아몬드 라이크 카본(DLC) 코팅 기술을 도입해 금형의 내구성을 대폭 향상시켰습니다. DLC 코팅은 금형 표면의 마모와 부식을 줄이는 데 효과적이며, 극한의 온도 변화에도 안정적인 성능을 제공합니다. 이를 통해 하야부사2는 계획된 예산과 일정 내에서 성공적으로 제작될 수 있었습니다. 이 사례는 사전 예방적 유지 보수와 첨단 기술 활용의 중요성을 잘 보여줍니다.
더불어, 하야부사2 프로젝트에서는 유지 보수 기록을 데이터화하고, 이를 바탕으로 금형 관리의 표준을 새롭게 정립했습니다. 이는 미래의 우주 프로젝트에서 동일한 문제를 방지하는 데 중요한 역할을 할 것입니다. 또한, JAXA는 이러한 경험을 바탕으로 다른 우주 탐사 프로젝트에서도 성공적인 금형 관리 기술을 확산시키고 있습니다.
4. 금형 유지 보수 기술의 미래와 우주 탐사에서의 적용 가능성
우주 탐사선의 금형 유지 보수를 위한 기술은 지속적으로 발전하고 있습니다. 미래에는 자율 로봇과 디지털 트윈 기술이 금형 관리의 핵심으로 자리 잡을 전망입니다. 디지털 트윈 기술은 금형의 가상 모델을 생성하여 실제 사용 조건을 시뮬레이션하고, 유지 보수 필요성을 사전에 예측하는 데 활용됩니다.
또한, 3D 프린팅 기술은 금형 자체를 현장에서 제작하거나 복구할 수 있는 가능성을 열어줍니다. 이 기술은 우주 환경에서도 작동할 수 있는 특수 프린터를 이용해 금형 손상을 신속히 복구하고, 탐사선의 운영을 중단 없이 지속할 수 있게 합니다. 이런 기술적 진보는 우주 탐사선의 제작 비용을 줄이고, 장기적인 우주 임무의 성공 가능성을 높이는 데 기여할 것입니다.
더 나아가, 인공지능 기반의 예측 유지 보수 시스템은 금형의 수명을 획기적으로 늘리는 데 기여할 것으로 보입니다. AI는 금형 사용 데이터를 분석하여 마모 가능성을 정확히 진단하고, 유지 보수 일정을 최적화합니다. 이러한 접근은 우주 탐사에서 발생하는 불확실성을 줄이고, 전체 프로젝트의 효율성을 높이는 데 필수적입니다.
우주 탐사선의 금형 유지 보수는 더 이상 단순한 기술적 도전이 아니라, 우주산업의 성공을 좌우하는 핵심적인 요소로 자리 잡고 있습니다. 이러한 기술 발전은 우주 탐사뿐만 아니라 지구상의 다양한 첨단 산업에도 긍정적인 영향을 미칠 것입니다.